Table of Contents
In today’s swiftly advancing world, modern industrial machinery stands at the forefront of innovation, driving efficiency and transforming how industries operate. This groundbreaking sector influences every aspect of our daily lives.
The Evolution of Industrial Machinery
Human ingenuity is reflected in the development of industrial machinery from crude hand tools to highly sophisticated automated devices. The majority of the machinery during the first Industrial Revolution (late 18th through early 19th centuries) was mechanical and powered by steam or water. These innovative devices greatly accelerated manufacturing, textile, and farming processes and paved the way for mass production.
Human ingenuity is reflected in the development of industrial machinery from crude hand tools to highly sophisticated automated devices. The majority of the machinery during the first Industrial Revolution (late 18th through early 19th centuries) was mechanical and powered by steam or water. These innovative devices greatly accelerated manufacturing, textile, and farming processes and paved the way for mass production.
Steam eventually gave way to electricity, sparking the second Industrial Revolution in the late 19th and early 20th centuries. Thanks in large part to industrialists like Henry Ford, assembly lines and mass production scales became commonplace during this time.
The third Industrial Revolution—also referred to as the Digital Revolution—was brought about by the development of computers and robots in the 20th century. Computer Numerical Control (CNC) machines, which offered unmatched accuracy and efficiency, were introduced during this era. The Internet of Things (IoT), artificial intelligence (AI), and cyber-physical systems are the hallmarks of the fourth Industrial Revolution, which is currently upon us. Continuous advancements in industrial machinery not only increase output but also open up new possibilities.
Automation and Robotics: A New Era of Efficiency
In the modern era, automation and robotics are the mainstays of industrial machinery, revolutionizing industries with increased precision and lower operating costs. This is about enhancing human labor, not replacing it. Automated systems will complete repetitive tasks more quickly, more accurately, and with less waste. For instance, in manufacturing, robots can now complete intricate tasks like assembling electronics, welding auto parts, and packaging products at speeds and precision that are not possible for human hands.
Furthermore, by handling hazardous jobs like handling poisonous materials or moving large objects, robotics enhances workplace safety by reducing the risk of accidents. Additionally, automation is essential in sectors like logistics.
In addition to these advantages, automation and robotics are crucial for the scalability of operations. Businesses can quickly increase production without imposing exorbitant labor costs, which allows them to react to market demands more quickly. Furthermore, these systems can learn and adapt continuously by combining AI and machine learning, which allows them to predict maintenance needs or modify procedures in response to changing circumstances. This raises the bar for industrial efficiency by prolonging the life of machines and ensuring their continuous high performance.
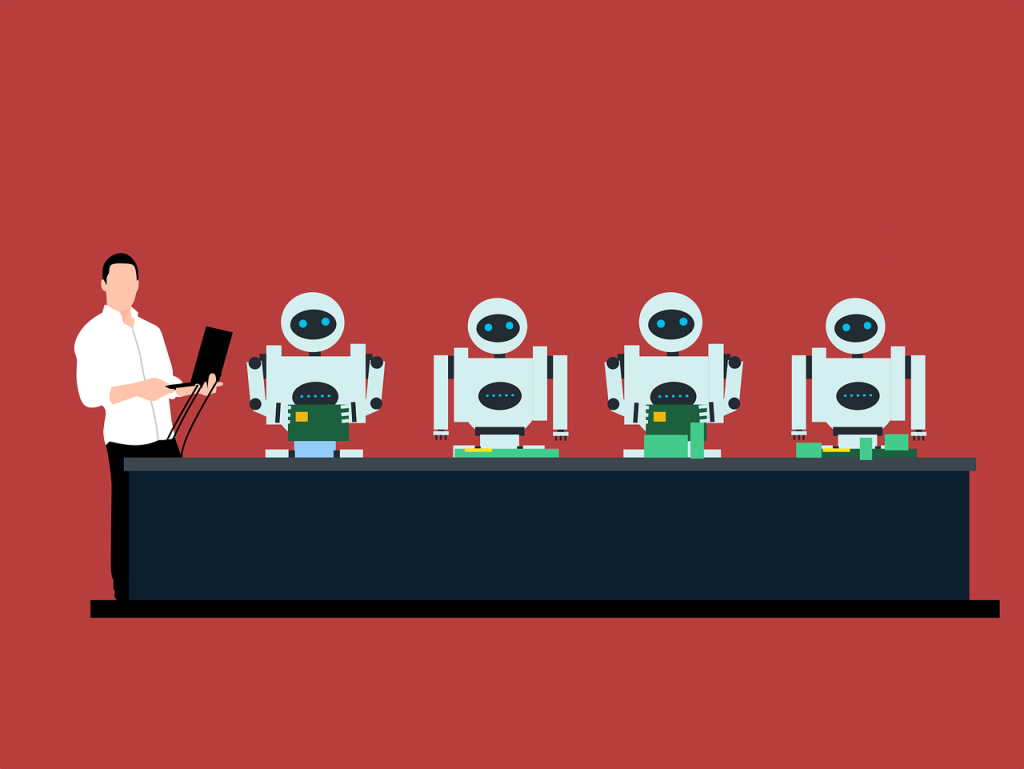
Sustainable Innovations in Industrial Machinery
Industrial machinery is using green technologies and sustainable practices to lessen its ecological footprint in line with the global emphasis on sustainability. Among the main innovations are energy-efficient designs that significantly reduce power consumption. Variable frequency drives, or VFDs, are now incorporated into industrial machinery designs to save energy by adjusting motor speed and torque in response to real-time demands.
The development of green materials and processes is another important advancement. For instance, additive manufacturing or 3D printing reduces waste significantly by using only the material required for production. In contrast, subtractive processes often result in significant material waste. Furthermore, machinery like shredders and compactors now play a significant part in recycling procedures.
Additionally, there is a strong push to develop equipment powered by renewable resources. Wind power systems and solar-powered machinery are becoming more widely available, which lessens reliance on fossil fuels. New monitoring systems that track emissions and energy use also make it easier to comply with environmental regulations by enabling industries to adjust their operations in real time to lessen their carbon footprint. In addition to benefiting the environment, these green innovations are also profitable because they often result in lower operating costs and improved company reputation.
The Role of Artificial Intelligence and IoT in Machinery
The industrial machinery environment is being transformed by artificial intelligence (AI) and the Internet of Things (IoT), creating a smart, networked environment that increases operational insight and efficiency. Large volumes of data collected by machinery sensors are processed by AI software algorithms, which identify patterns and predict outcomes that were previously unthinkable. By anticipating equipment failures before they occur, this predictive maintenance feature reduces maintenance costs and downtime.
IoT goes one step further by connecting equipment and devices online, enabling remote monitoring and real-time data sharing. Accurate monitoring of operational parameters such as temperature, pressure, and vibration levels is made possible by the connectivity. Any departure from the typical range triggers an alarm, requiring quick fixes and preventing any potential interruptions. For instance, IoT-enabled sensors in a packaging factory can verify that, without human intervention, machines fill and seal products according to the correct specifications, upholding quality standards.
IoT and AI work together to create digital twins, which are virtual representations of real systems used for analysis, optimization, and simulation. Manufacturers can improve processes without running the risk of trial and error in the real world by simulating changes in a virtual environment and predicting how they will affect the actual system. Additionally, sophisticated machine learning algorithms adapt to the unique operational characteristics of specific environments, gradually improving performance. Together, these technologies propel industrial machinery into an intelligent automation future that will increase productivity and efficiency like never before.
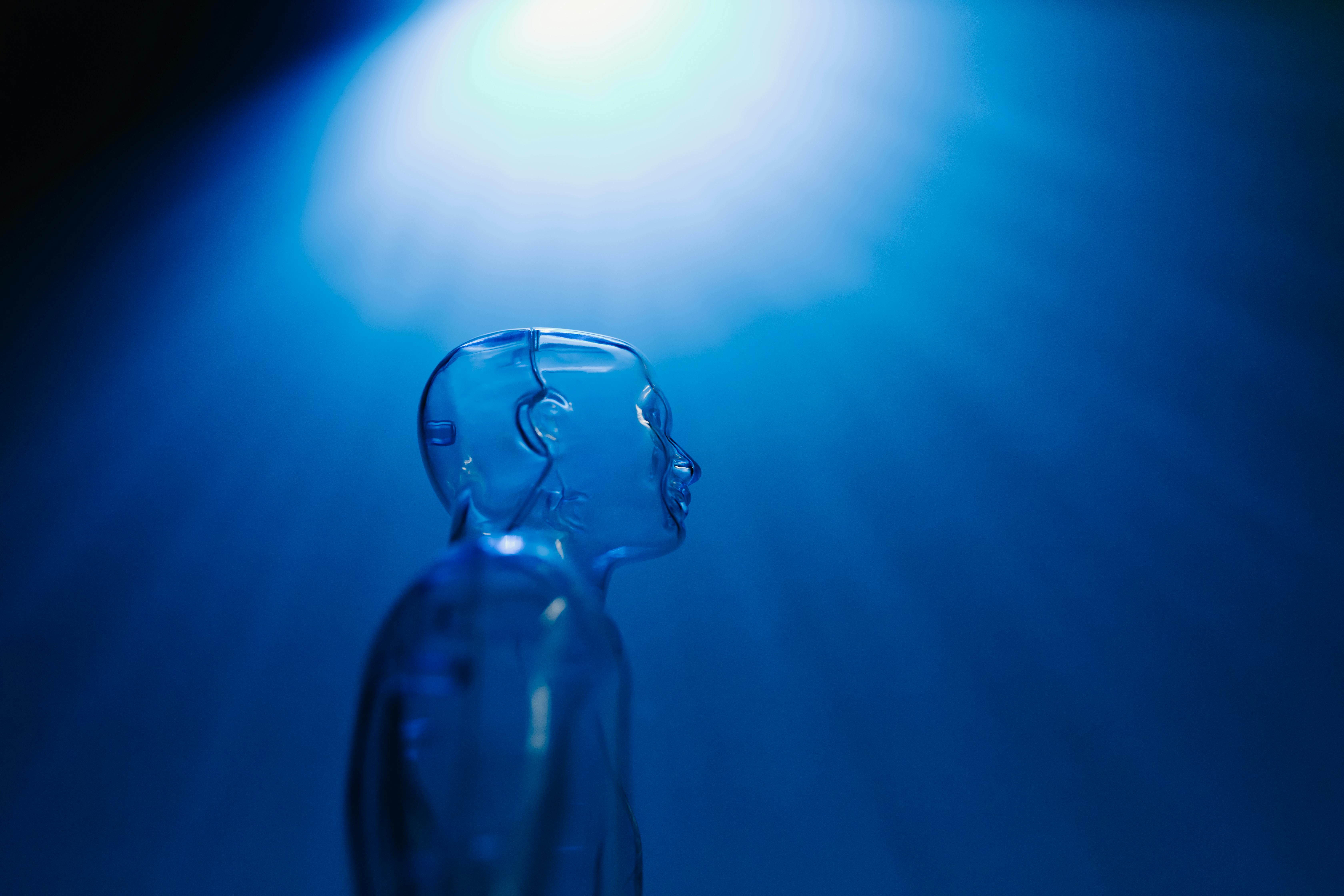
Challenges and Future Prospects of Industrial Machinery
Notwithstanding the remarkable advancements, the industrial machinery sector faces several obstacles that could influence its future. The high upfront costs of the newest technologies, like artificial intelligence, the Internet of Things, and robotics, are a significant obstacle. These expenses may be difficult for small businesses to absorb, increasing the gap between lower-capitalized companies and industry giants. These technologies&8217; adoption also necessitates highly specialized skill sets, which poses a significant workforce reskilling challenge. Comprehensive training and education programs are necessary to close this skills gap, and industry, educational institutions, and the government must work together.
Another crucial issue is cybersecurity, especially as equipment gets more networked. It is crucial to protect sensitive data and ensure that networked systems run securely against cyberattacks. Industrial control systems are frequently the focus of hostile attacks, which could disrupt operations or lead to a significant data breach. Implementing strict cybersecurity protocols is a continuous process that calls for focus and consistent funding.
Innovation doesn&8217;t seem to be slowing down in the future. Quantum computing developments could make previously unheard-of processing power available for complex industrial simulations and optimizations. We can anticipate even more sophisticated automation capabilities as AI advances, possibly even enabling machines to learn and optimize themselves on their own.
One promising avenue is the use of collaborative robots, or cobots, to support and cooperate with people. Cobots can complete tasks in collaborative workspaces, fostering human-machine collaboration, in contrast to traditional robots that operate independently. Furthermore, ongoing research and development in sustainable technologies and renewable energy will inevitably result in new developments that will further align industrial machinery with environmental goals. Industrial machinery is expected to become more intelligent, integrated, and sustainable in the future, further contributing to global development.